An Overview of the Different Methods Used in Testing HDPE Pipes
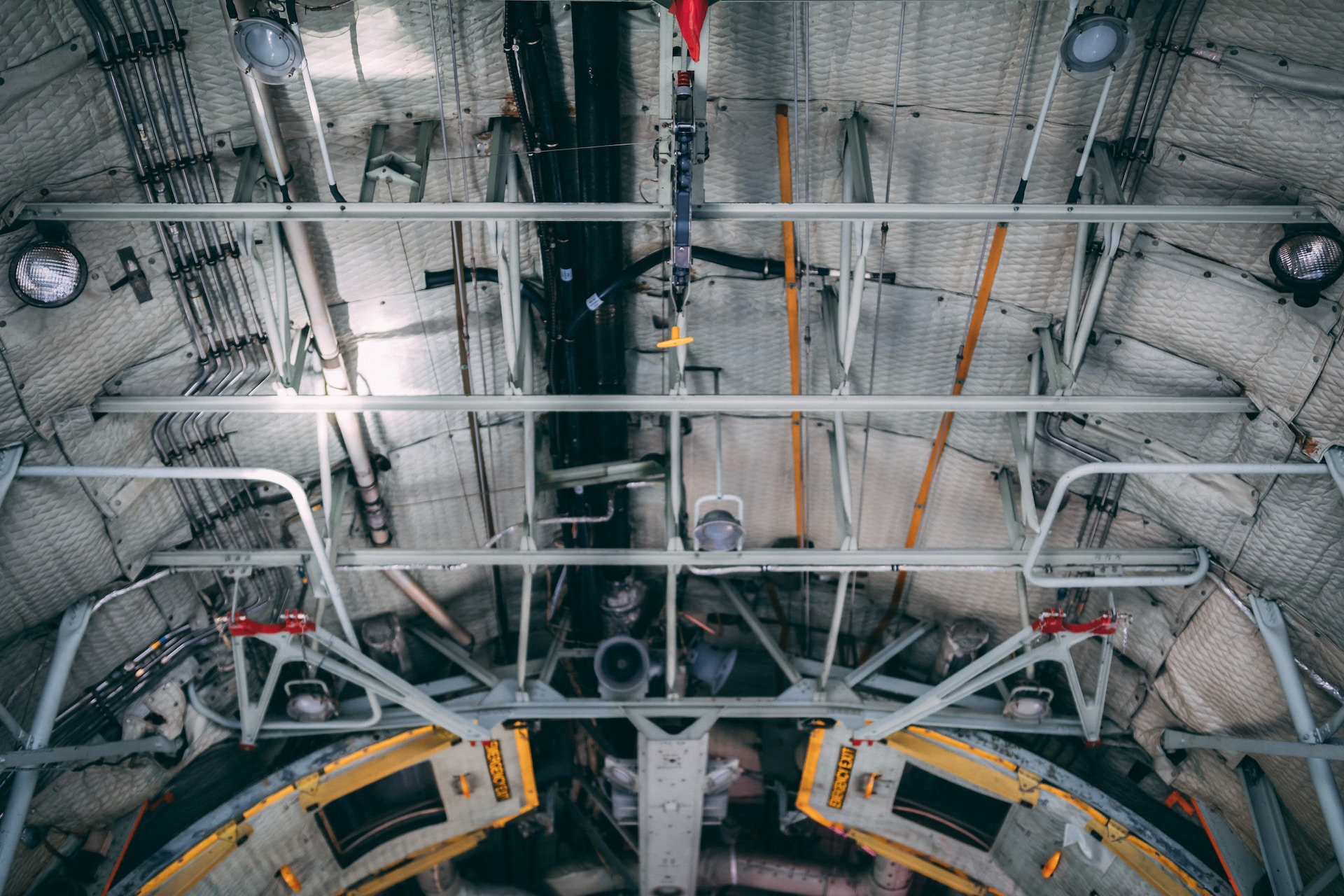
Photo by Hanson Lu on Unsplash
High-density polyethylene (HDPE) is a popular plastic pipe material for high-demand underground and above-ground applications. HDPE piping applications include potable water transport, irrigation, drainage, sewage handling, gas distribution, chemical waste management, and firefighting.
HDPE pipes testing is recommended during installation to ensure the longevity of piping systems. Field testing primarily puts HDPE pressure pipe connections to the test. If you know the saying, “A chain is only as strong as its weakest link?” you must realize that a pipeline is only as strong as its weakest connection.
How do you test HDPE pipes? You may use the following procedures to test for pressure leaks.
Hydrostatic Pressure Testing
Hydrostatic pressure testing is a field test procedure typically indicated during potable water line installation. Hydrostatic HDPE pipe testing may be done inside or outside the trench. It accomplishes the following:
- Assesses the structural integrity of the pipeline
- Tests the fusion of the pipes and fittings
- Reveals faults or defects in the pipe laying and embedment procedures
- Reveals faults or defects in the assembly of piping components (e.g., tapping bands, saddles, flange sets, mechanical joints)
- Ensures that the pipeline will not leak when operating pressure exceeds the pipe design pressure
Hydrostatic pressure testing is typically done by sections. You may use the F2164 specifications of the American Society for Testing Materials (ASTM) to perform hydrostatic testing of HDPE pipes.
Follow these procedures when testing outside the trench.
- Secure the test section against movement to prevent accidents.
- Gradually fill the test section with water and bleed out any air trapped inside the line.
- Pump in as much water as needed to attain the specified testing pressure (STP), which can be up to 1.5 times the pipe design pressure.
- Maintain pressure at STP for a maximum of three hours; add water as needed to maintain STP.
- During this time, visually inspect the line, especially the joints, for integrity.
Follow these procedures when testing inside the trench.
- Secure the test section against movement to prevent accidents.
- Gradually fill the test section with water and bleed out any air trapped inside the line.
- The HDPE pipes will naturally stretch to accommodate the water. Compensate for the initial stretching by adding water as needed. The goal is to maintain pressure at STP, which can be up to 1.5 times the pipe design pressure.
- After about four hours of maintaining STP, begin the testing phase.
- Maintain STP for one to three hours (do not exceed three hours). During this test phase, water should be pumped in as needed. Note the amount of make-up water required to restore STP at every hour interval and compare it with the water volume indicated in the standard allowance for expansion under test pressure chart. It is a pass if the volume of make-up water remains within acceptable values.
Alternatively, instead of measuring make-up water volume during the test phase, do this in lieu of step five above.
After maintaining STP for four hours, decrease pressure by 10 psi and measure how much pressure remains after one hour. It is a pass if the pressure is within 5% of STP.
Pneumatic Leak Testing
Pneumatic leak testing, also known as air testing, is a pressure leak test like hydrostatic testing. However, it uses air or gas instead of water or some other hydrotesting liquid.
Pneumatic leak testing is used mainly when the typical hydrostatic test is impractical, as in the case of piping systems that:
- Have internal linings that water may damage
- Must remain free of moisture (say, those that carry refrigerant)
- Have been laid out or assembled on a supporting structure that cannot take hydrostatic testing loads and conditions
Pneumatic leak testing failures can be extremely violent due to the sudden release of compressed gas. Follow the safety procedures outlined in ASTM F2786, the specification that provides the standards for field pneumatic leak testing of PE pressure piping systems.
Pneumatic leak testing generally follows these procedures.
- Gradually fill the system with gas until the pressure level reaches 10% of the leak test pressure (LTP).
- Disconnect from the gas filling and pressurizing equipment and examine the test section for leaks. This can be done visually or by measuring the pressure after one hour. It’s a pass if the pressure stays within 5% of the test phase pressure.
- Reconnect the filling and pressurization equipment to the test section and gradually increase pressure in 10%-of-LTP increments until it reaches 50% of LTP.
- Repeat step two.
- Reconnect the pressurizing equipment and gradually increase the pressure by 10%-of-LTP increments until you reach 100% maximum test pressure (MTP). Note that MTP is the lower value between the LTP and the pressure rating of the lowest pressure-rated component in the system. LTP is calculated using a formula outlined in the ASTM F2786 specification.
- Repeat step 2.
- If the system fails, the test section must be depressurized before any repairs are attempted.
Other Methods for HDPE Pipes Testing
The strategies for HDPE pipes testing are not limited to the hydrostatic and pneumatic leak tests outlined above.
Deflection testing measures HDPE pipe flexibility or its ability to deflect or assume an oval shape without structural damage in response to stress. HDPE pipes must deflect to take advantage of backfill support.
Joint testing, which is crucial in gravity sewer systems, may also be done to check for infiltration (estimates the amount of fluid the system will retain and convey to the water treatment facility) and exfiltration (estimates the amount of sewage the system will leak to the surrounding soil). Exfiltration may be done using air and water exfiltration testing, while infiltration may be done through water infiltration testing.
Testing HDPE Piping Systems
HDPE pipe fittings, pipes and systems must be tested in the field upon or during installation to ensure they’ll serve their purpose and attain their expected lifespans. Testing also minimizes the risk of costly repairs and replacements.
However, ensuring structurally durable piping systems begins with obtaining pipes and pipe fittings that pass internationally established manufacturing standards and installing and assembling them according to industry best practices.
Polyfab Plastic Industry LLC is a leading manufacturer of HDPE and polyvinyl chloride (PVC) pipes and a top provider of HDPE installation services in the UAE. Contact us to learn about our plastic pipes and take advantage of our turnkey end-to-end piping installation solutions and expertise.
We're here to help
Let our specialists help you find the right piping products for your needs. Get access to expert services and top-of-the-line supplies for quality, on-time, professionally delivered projects. Get in touch with the Polyfab team today.